categoria: Vendere e comprare
Emilia da export, Flash Battery e il metodo Kaizen nella Motor Valley
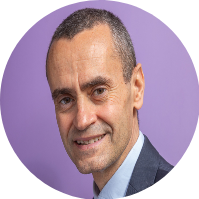
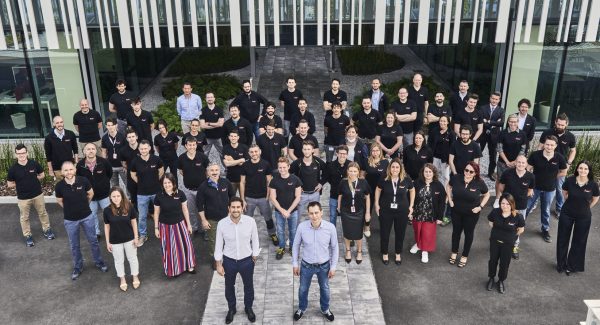
Partiamo dai dati per poi andare a un caso concreto, quello di Flash Battery: l’export dell’Emilia-Romagna si colloca oggi quasi sette punti percentuali al di sopra di quello del 2019, quando fu stabilito il record regionale. Nel primo semestre, infatti, le esportazioni hanno toccato – come ha sottolineato l’Istat pochi giorni fa – quota 35,36 miliardi, due miliardi in più di quanto raggiunto nel 2019. I migliori risultati sono stati registrati in Asia (+40,7%), in Oceania (+37) e nell’America del centro-sud (+32).
IL CASO FLASH BATTERY: 65 DIPENDENTI CON MENO DI 35 ANNI
E veniamo a un caso concreto di successo, quello di Flash Battery, l’azienda di Sant’Ilario d’Enza in provincia di Reggio Emilia nata in un garage nel 2012 grazie a due amici, l’economista Marco Righi e l’ingegnere Alan Pastorelli, rispettivamente CEO (nonché presidente dei giovani imprenditori di Reggio Emilia e vicepresidente di Unindustria) e CTO.
Specializzata nella produzione di batterie al litio per macchine industriali e veicoli elettrici, l’impresa reggiana ha inaugurato, alla presenza del presidente della Regione Stefano Bonaccini, la nuova sede: 20 mila metri quadrati (con un’area produttiva di 3.200 metri quadrati), 65 dipendenti con età media inferiore ai 35 anni, 17,5 milioni di fatturato previsti a fine 2021 con una crescita del 30% rispetto al 2020.
EXPORT IN 54 PAESI, PARTERNSHIP CON EFA FRANCE E ATECH GMBH
Un dato non deve – per tornare al discorso iniziale relativo all’export dell’Emilia – passare inosservato: Flash Battery esporta in 54 Paesi ed è partner di alcune importanti realtà del mondo industriale, della ricerca e dell’università anche nell’ambito di rilevanti progetti varati dall’Unione Europea (con investimenti complessivi per oltre un miliardo di euro) per il passaggio a un continente a zero emissioni di carbonio entro il 2050. Parliamo, pensando alle partnership, a EFA France e alla tedesca ATECH GMBH per lo sviluppo di progetti di elettrificazione in Europa. L’export di Flash Battery, torniamo al punto di partenza, è cresciuto negli anni, rappresentando oggi il 30% del fatturato.

La nuova sede di Flash Battery a Sant’Ilario d’Enza in provincia di Reggio Emilia
METODO KAIZEN NELLA MOTOR VALLEY: MIGLIORARSI OGNI GIORNO
Dietro a questi numeri c’è un metodo di lavoro ispirato al “continuous improvement”. Non è un caso che nell’area dedicata al collaudo delle batterie, su una lavagna, a Sant’Ilario d’Enza siano indicate queste tre parole chiave: obiettivi, persone e kaizen, dal nome del metodo sviluppato in casa Toyota grazie all’ingegnere meccanico Taiichi Ohno. Parola giapponese, appunto, traducibile in italiano come “cambiare per il meglio”.
È Masaaki Imai, fondatore del Kaizen Institute, a riassumere i tre pilastri della filosofia giapponese: anzitutto i risultati di un’organizzazione possono essere migliorati agendo sui comportamenti degli individui; secondariamente le persone desiderano fare un lavoro di qualità, ma vanno messe in grado di farlo rimuovendo eventuali barriere e rigidità organizzative; infine, gli standard non devono essere presentati come regole rigide, ma come strumenti di conoscenza affidati alle persone affinché li conoscano e facciano propri.
L’ESEMPIO TOYOTA: DIPENDENTI PROTAGONISTI DEL PROGRESSO
«Nel sistema Toyota – sottolinea Alberto Portioli, docente di Operations management al MIP Politecnico, la business school milanese – gli operatori hanno la facoltà di modificare la procedura migliorandola. Anzi, sono invitati a farlo. Il fatto di poter modificare la procedura, da un lato toglie il senso di essere solamente un esecutore, perché si ha la possibilità di fare diversamente, se si trova una procedura migliore. Se non la si trova, o fintanto che non la si trova, quella esistente è la migliore nota, e l’operatore per fare bene il proprio lavoro la fa propria».
Se il fordismo ha creato un sistema di successo all’inizio dello scorso secolo, separando chi decide cosa fare da chi lo fa, «il sistema Toyota – tira le somme Portioli – ha riunificato nell’operatore la decisione di cosa fare e l’azione di realizzarlo, come era nella produzione artigianale, e questo aumenta l’orgoglio per quello che si sta facendo».
LA VIA DEL MIGLIORAMENTO: PIANIFICARE, SPERIMENTARE, MISURARE E DEFINIRE NUOVI STANDARD
«Il ruolo di tutti i dipendenti di Flash Battery – racconta Righi – non è solo quello di svolgere mansioni, ma anche di migliorarle, realizzandosi professionalmente e personalmente, e allo stesso tempo contribuendo al miglioramento dell’azienda». È il miglioramento continuo dell’Emilia, che vede protagonisti i dipendenti. Plan, do, check e act: è la celebre ruota teorizzata dall’ingegnere americano Edward Deming, promotore di studi sul miglioramento della produzione.
Le aziende che vogliono progredire devono percorrere cicli di problem solving strutturati in più fasi: “plan” o “pianificazione” di interventi e azioni mirate al miglioramento; “do” o sperimentazione; “check” o “misurazione e valutazione” dei risultati; e, infine, “act” o “definizione e comunicazione dei nuovi standard”. Così, pianificando, sperimentando, misurando e definendo nuovi standard Flash Battery è cresciuta ritagliandosi uno spazio da protagonista nel mercato delle batterie al litio. L’ha fatto facendo leva sulla capacità dei lavoratori (giovanissimi, come racconta la loro età media), del loro cuore e del loro cervello.
Twitter @filippo_poletti